Stainless Steel Crimped Wire Mesh-Stainless Steel Corrugated Mesh
With a meticulous focus on precise engineering, our stainless steel crimped wire mesh comes in varied specifications, catering to a diverse array of applications. From different mesh sizes to varying wire diameters, we endeavor to meet our clients' varied needs with absolute precision and customization.
Stainless steel corrugated mesh, also known as stainless steel crimped mesh. Harnessing the robustness of various stainless steel grades such as 304, 316, and 316L, our meshes boast distinguished properties and corrosion resistance, safeguarding your investments and ensuring longevity even in the most rigorous environments.
Stainless steel crimped wire mesh is a type of woven wire mesh that is made from stainless steel wires. It is characterized by its unique crimped or wavy pattern, which is achieved by alternating the weaving of the wires. This crimping process provides the mesh with added strength and stability.
Stainless steel crimped wire mesh offers excellent corrosion resistance, durability, and strength. It can withstand harsh environments, high temperatures, and exposure to chemicals without rusting or corroding easily. This makes it suitable for a wide range of applications.
Applications
- Vibrating tray screens
- High pressure filters
- Cooling circuit filters
- Grids and trays for thermal treatments
- Decoration
- Industrial Uses: Including filtration, separation, protection, etc.
- Architectural Uses: Utilized for decorative purposes, façade treatments, or safety barriers.
- Agricultural Uses: Employed in animal fencing or as barriers.
316 stainless steel has better corrosion resistance than 304 stainless steel.
The crimped pattern of the mesh enhances its filtering and sieving capabilities. It effectively retains particles and ensures efficient flow of liquids or gases. This makes stainless steel crimped wire mesh suitable for various applications including filtration, screening, separation, and protection.
The mesh size or opening size can vary depending on the specific requirements of the application. Stainless steel crimped wire mesh is available in different grades of stainless steel, such as 304, 316, and 316L. Each grade has its own specific properties and corrosion resistance levels.
Stainless steel crimped wire mesh is a versatile and reliable material that offers excellent corrosion resistance, durability, and strength. It is widely used in industries such as mining, construction, food processing, pharmaceuticals, and agriculture.
The manufacturing process of stainless steel crimped mesh generally involves a series of stages that transition from raw material (stainless steel wire) to a finished crimped mesh.
Here's a simplified breakdown of the process:
- Wire Selection: Choose high-quality stainless steel wire with the desired properties (anti-corrosion, high tensile strength, etc.).
- Drawing Process: The selected stainless steel is drawn through a series of dies to reduce its diameter and achieve the desired wire size.
- Wire Annealing: To make the wire flexible and ductile, it might be annealed. Annealing involves heating the wire and then slowly cooling it.
- Pre-crimping: Before weaving, wires are often pre-crimped. Crimping involves bending the wires into a series of waves or curves. Roller Crimping: The wire is passed through two rollers with a zigzag pattern to create a crimped form.
- Hydraulic Crimping: Hydraulic presses may also be used to force the wire into the desired crimped shape.
- Arrangement: The crimped wires are arranged perpendicularly to form the desired mesh aperture (size of the opening).
- Warp and Shute Wires: The warp wires (vertical) and shute wires (horizontal) are interwoven, using one of several techniques depending on the desired mesh characteristics.
- Weave Styles: Common styles include plain weave, twill weave, or Dutch weave. Each weave style offers different characteristics in terms of strength, flexibility, and filtration capacity.
- Mesh Cutting: Once woven, the mesh is cut into sheets or rolls as per customer requirements using specialized cutting tools.
- Forming: The mesh might be formed or shaped into specific products or components, such as filters, baskets, or screens.
- Testing: Various tests, such as tensile testing, aperture size checking, and corrosion testing, are performed to ensure the mesh meets the desired specifications and quality standards.
- Visual Inspection: The mesh is examined for any defects or inconsistencies in the weave.
- Cleaning: The mesh may be cleaned to remove any lubricants or residues from the manufacturing process.
- Surface Treatment: Depending on the application, the mesh may receive surface treatments, such as passivation, to enhance its corrosion resistance.
- Packing: The mesh is securely packed to avoid damage during transit.
- Shipping: Finally, the mesh is dispatched to customers or to a site for utilization in various applications.
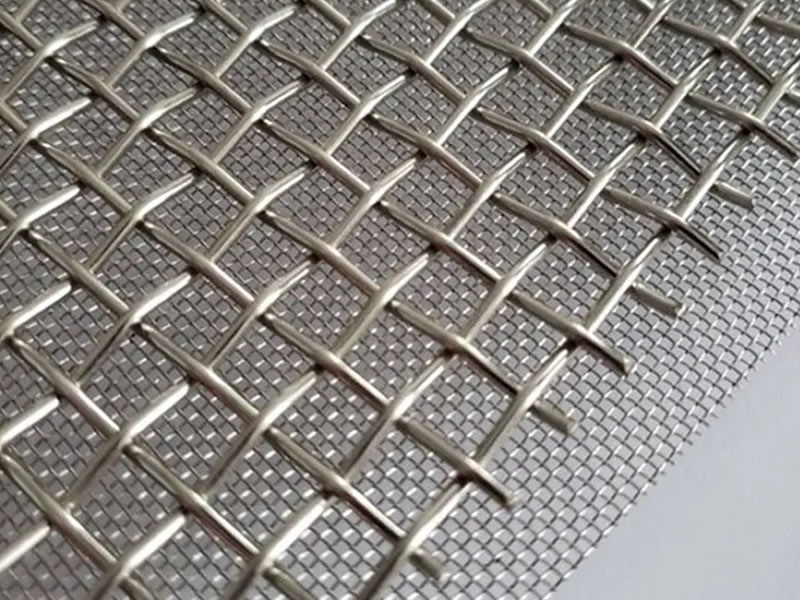
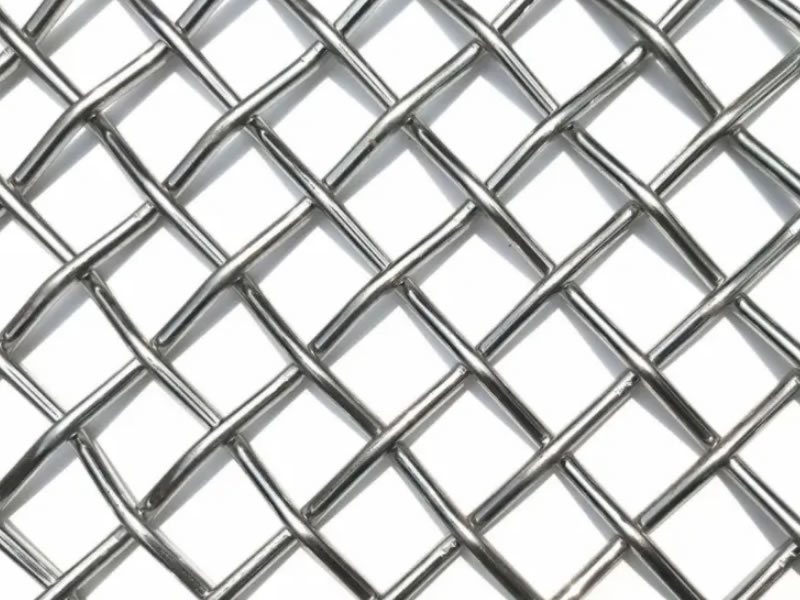
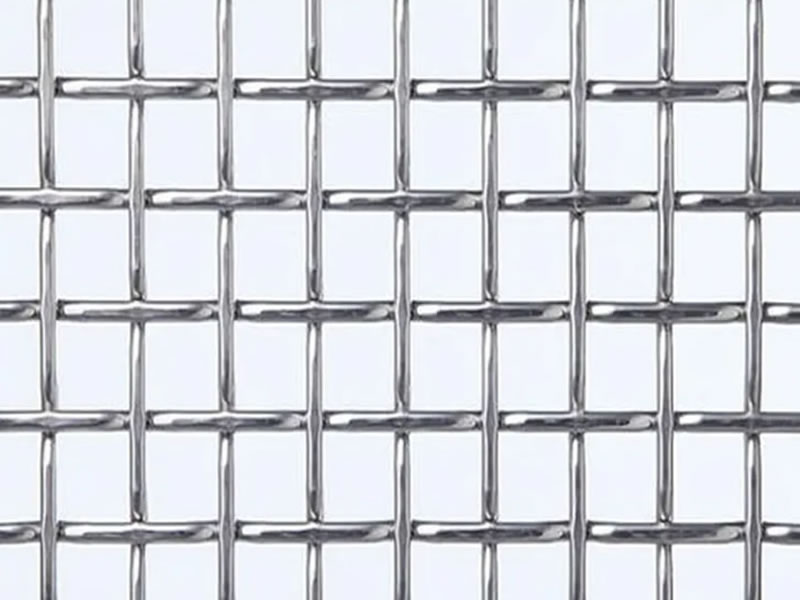
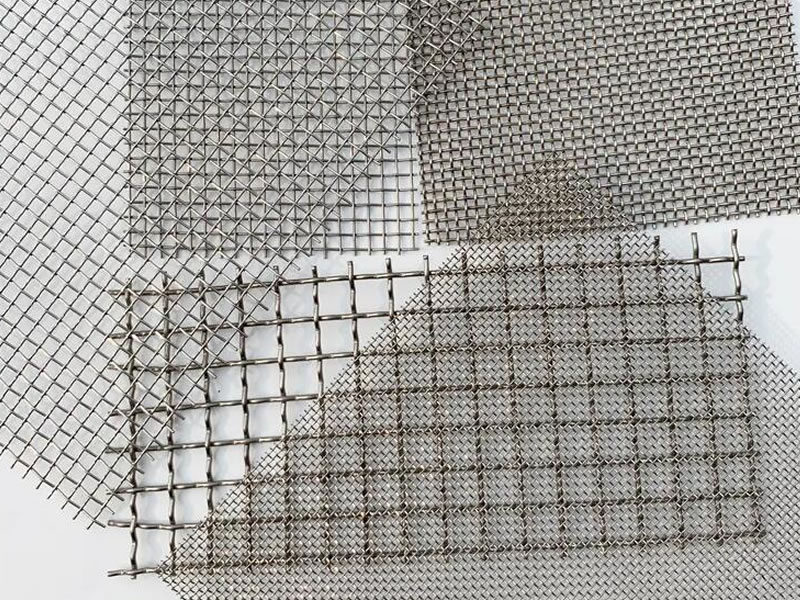
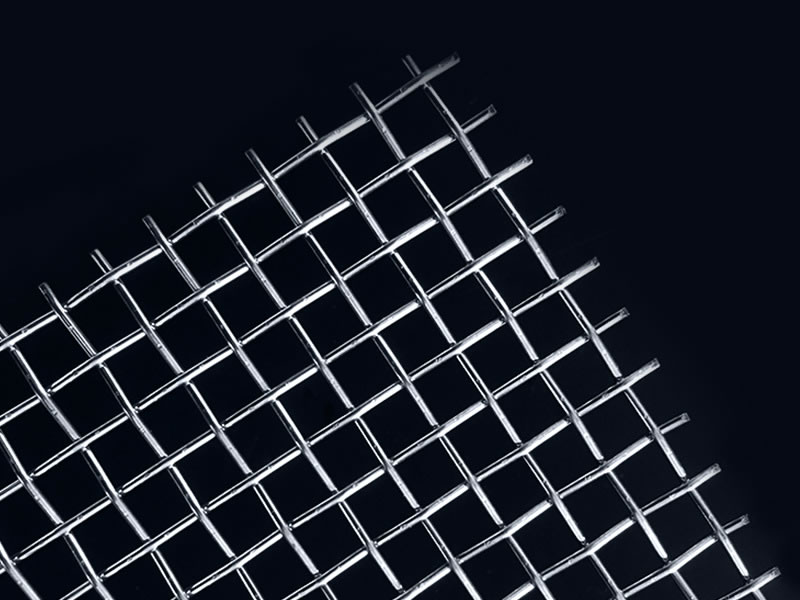
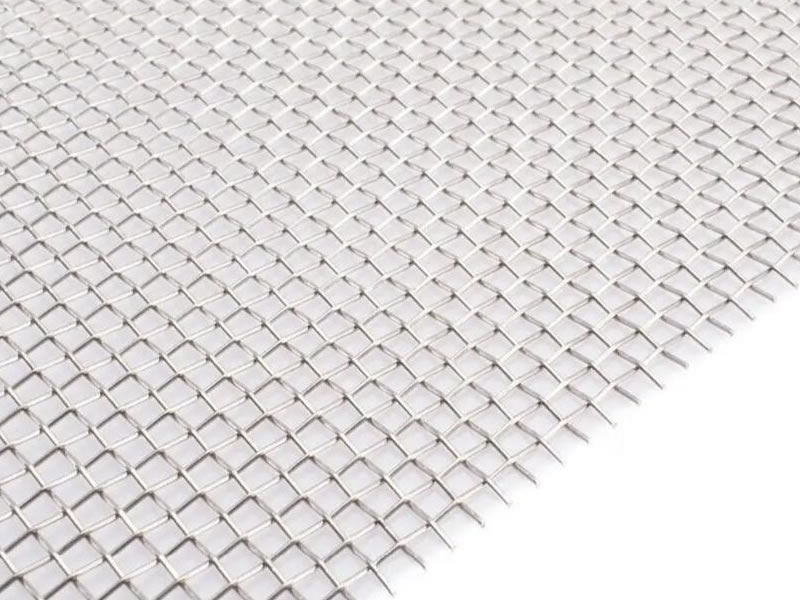